
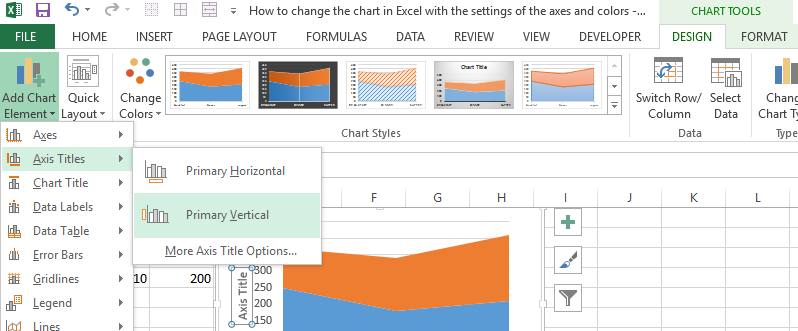
pressure drop in air filters and the return air fan selection and motor kilowatt should cater to the required return air flow rate against a total static pressure of 50–55 mm w.g. Since the pressure drop in rotary drum filters when dirty can be as high as 30 mm w.g, the return air fan selection in mill humidification applications should account for up to 25 mm w.g. Return air fans are sized to re-circulate up to 95% of design supply air quantity for each department, by considering the design static pressure required to overcome pressure drop in the return air floor grilles, masonry return air trench, rotary drum type return air filters, return air dampers, etc. Design static pressure for supply air fan selection can vary from 40 mm to 55 mm w.g depending on the air washer length, spray headers and eliminators design, other internal components including heating coils, if any, design air velocity etc. Normally high efficiency axial flow fans, with aluminium impellers, adjustable pitch aluminium blades with direct drive totally enclosed motors are selected to deliver the design supply air quantity against the required static pressure, after considering pressure drop in fresh air damper, air washer internals, washer–dampers, supply air ducting, and supply air diffusers with volume control dampers. Also by increasing the thickness and curvature of the inner sections, the blades can be made stiffer this limits flutter and allows the impellers to be run at higher speeds.

As compared to curved sheet blades, aerofoils can apply greater force to the air, thereby increasing maximum pressure and can maintain better efficiency over a wider range of volumetric flow.
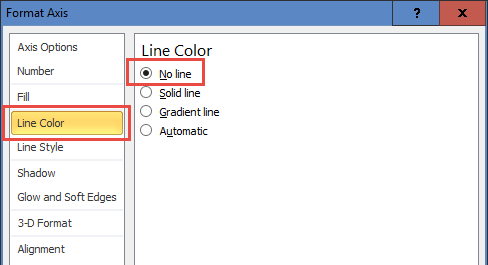
Impellers usually have blades with cross sections matching those of an aerofoil. The air delivering capacity of axial flow fans ranges from 100 to 500000 cubic feet per minute (3 to 14000 cubic meters per minute). The blade force necessarily has an additional component in the tangential direction, providing the reaction to the driving torque: this sets the air spinning about the axis independently of its forward motion. The primary component of blade force on the air is directed axially from inlet to outlet and thus provides the pressure rise by a process that may be called direct blade action. In a typical axial fan, the effective progress of the air is straight through the impeller at a constant distance from the axis.
